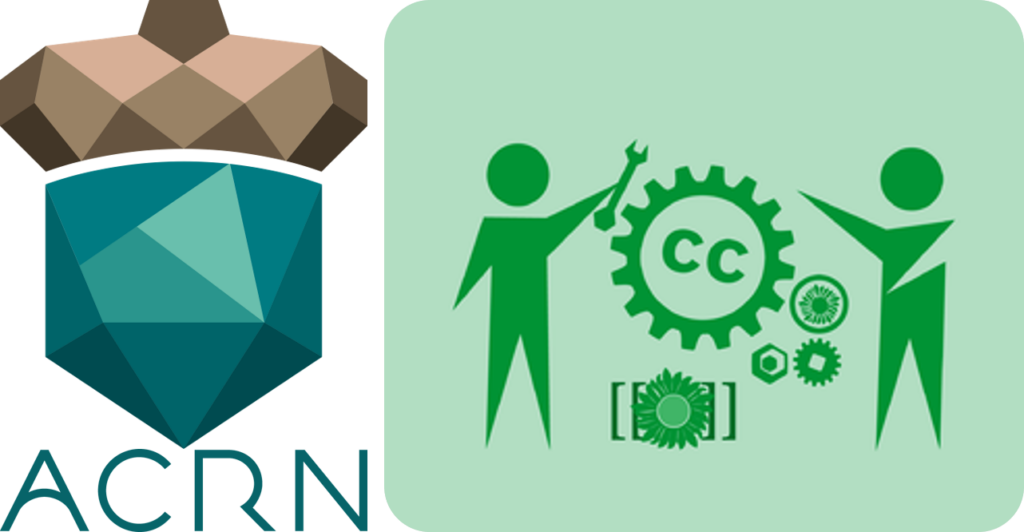
The ACRN team is hosting a free two-day virtual Meet-Up, brought to you by Intel. Please join us 25-26 May, to learn more about ACRN, how far it has come over the last three years, and where it is headed. The Meet-Up is intended for developers with a technical profile and interest in hypervisor solutions, but no prior knowledge of ACRN is required.
Date: Tuesday, 25th of May, 2021
Time: 9AM to 1PM (Central European Time)
9:00AM | Welcome |
9:10AM | ACRN Introduction and Architecture |
9:50 AM | Real-Time Management and Performance Optimization |
10:30 AM | Functional Safety Design and Certification Plan |
11:10 AM | Break |
11:30 AM | Installation and Configuration Introduction |
12:10 PM | Enabling ACRN on New Hardware Platforms |
12:50 PM | Conclusions |
1:00 PM | End |
Date: Wednesday, 26th of May, 2021
Time: 9AM to 1PM (Central European Time)
9:00AM | Welcome |
9:10 AM | Orchestration with Libvirt and Kata Container |
9:50 AM | Boot Process and Secure Boot |
10:30 AM | Community & Development Model |
11:10 AM | Break |
11:30 AM | Debugging ACRN (Tracing & Logging) |
12:10 PM | Inter-VM Communication Introduction |
12:50 PM | Conclusions |
1:00 PM | End |
Here’s the link to register and get an invitation to attend. We hope to see you there!
We are pleased to announce the release of ACRN™ hypervisor version 2.4.
What’s New in v2.4
Extensive work was done to redesign how ACRN configuration is handled, update the build process to use the new configuration system, and update the corresponding documentation. This is a significant change and improvement to how you configure ACRN but also impacts existing projects, as explained in the next section.
We’ve also validated the hybrid_rt scenario on the next generation of Intel® Core™ processors (codenamed Elkhart Lake) and enabled software SRAM and cache locking for real-time performance on Elkhart Lake.
See the v2.4 full release notes and documentation for more information about this release including fixed and known issues.
On January 6th, ADLINK announced that their ROScube-I ROS 2 controller, powered by Intel technology, is one of the first robotic controllers to support ACRN™ real-time hypervisor. The ACRN community congratulates the ADLINK team on this important milestone that allows mixed real-time and application workload consolidation on a single Edge platform.
ACRN is a flexible, lightweight reference hypervisor that optimizes and streamlines embedded development through an open-source platform. Built with real-time safety in mind, ACRN defines a device hypervisor reference stack and an architecture for running multiple software subsystems (as shown below), managed securely on a consolidated system using a virtual machine manager (VMM). ACRN hypervisor takes advantage of Intel Virtualization Technology (Intel VT) and supports User VM and Service VM to run a User OS and Service OS, real-time VM (RTVM), and is designed to run a real-time OS, such as Xenomai. Because of its real-time capability, RTVM can be used for soft programmable logic controller (PLC), inter-process communication (IPC), and robotics applications.
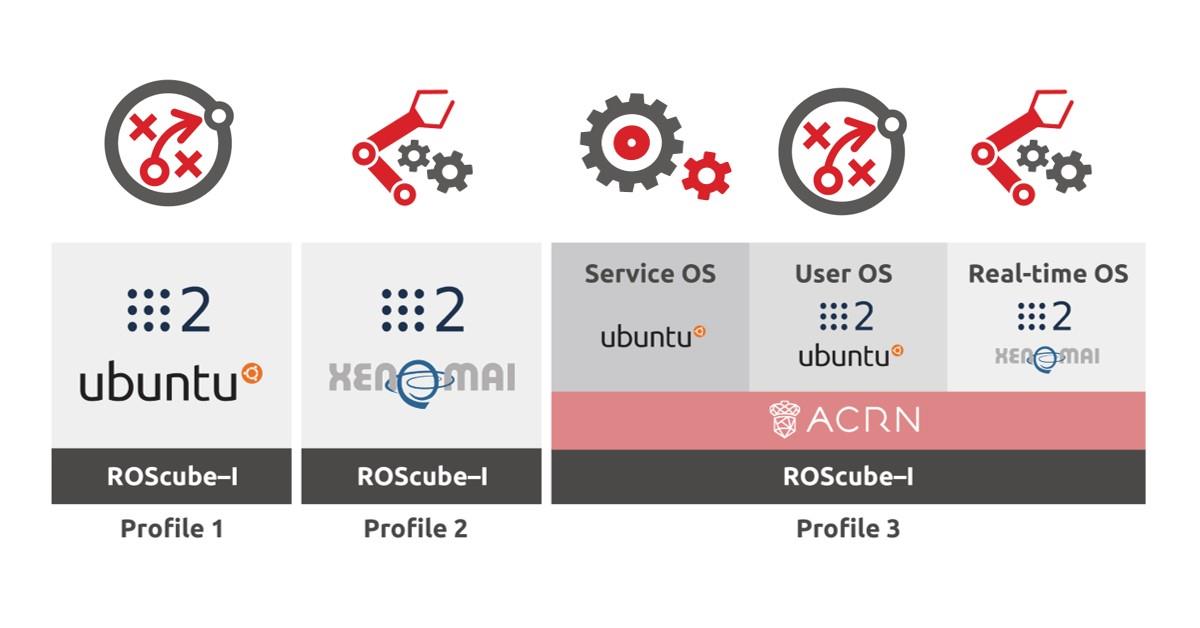
Read more about getting started with ACRN on the ADLINK ROScube-I in the ACRN documentation: https://projectacrn.github.io/latest/getting-started/roscube/roscube-gsg.html
“ADLINK’s adoption of ACRN is a great testimonial to the maturity of the project, as an open-source real-time hypervisor for the most demanding applications,” said Eddie Dong, Project ACRN’s architect and maintainer. “The collaboration between ADLINK and Project ACRN has been a true win-win situation; using ACRN hypervisor to consolidate heterogeneous workloads brings added value and unleashes the computing power of the ROSCube-I platform. It puts ACRN at the heart of a commercial solution for industrial customers.”
“Virtualization is especially important in industrial environments because of device and application longevity. Virtualization enables factories to modernize their robot control system hardware by using VMs to run older control systems and operating systems far beyond their intended retirement dates,” said Dr. Ryan Chen, Director of the Advanced Robotic Platform Group at ADLINK. “Our customers can leverage this technology on our ROScube-I controller, for example, to run human-machine interfaces (HMI) in User OS, run artificial intelligence (AI) in Service OS and leave some compute function running on soft programmable logic controllers (PLC) that require hard real-time characteristics. This gives customers the ultimate in future-proof flexibility and reliability, allowing them to scale up development.”
“Robotic controllers based on Intel hardware and software platforms enable flexible, reliable and scalable solutions for some of the most advanced robotics applications. Real-time hypervisors, Intel Distribution of OpenVINO toolkit and Intel architecture make it easy to integrate data, devices, and processes while improving operational efficiency. Intel and ADLINK are both active contributors to the ROS 2 community and it is great to see this work in action,” said Brian McCarson, Vice President, Internet of Things Group at Intel Corporation.
Check out the ADLINK full press release for more details: https://www.adlinktech.com/en/News/ADLINK-ROScube-I-ROS-2-controller-now-with-ACRN-real-time-hypervisor
ACRN to be used in industrial applications on the Nerve Blue edge computing platform
VIENNA and SAN FRANCISCO, Dec. 9, 2020 — IoT Solutions provider TTTech Industrial today is launching the first commercial product based on the Linux Foundation’s ACRN™ hypervisor for the industrial market. With the latest release of its Nerve Blue industrial edge computing platform, TTTech Industrial is making ACRN 2.0 available to customers in a commercial, fully supported software solution that runs on a variety of Intel processors in an array of industrial applications. ACRN Project members include ADLINK, Aptiv, Intel Corporation, LGE and Neusoft Corporation.
ACRN™ is a flexible, lightweight reference hypervisor built with real-time processing and safety-criticality in mind. When developing ACRN 2.0, the community prioritized three key requirements for hypervisors in the Industrial IoT and edge environments: functional safety, real-time processing and resource sharing for additional flexibility. TTTech Industrial and Intel are actively engaged in the project and have worked together to shape ACRN technology and rapidly integrate it into the Nerve Blue edge computing platform.
“The ACRN community is accelerating embedded development for the integration of heterogenous, real-time applications in edge environments. This milestone really represents what the technical features that set ACRN apart,” said Mike Dolan, General Manager and Senior Vice President of Projects, Linux Foundation. “As the project and integrations mature, we expect even more contributions and innovations to result from this open source collaboration.”
Nerve Blue’s integration of ACRN 2.0 allows it to run PLC software for controlling high-speed machine functions alongside other less time-sensitive software applications on the same hardware platform. Nerve Blue leverages ACRN 2.0’s unique features and optimizations to create special virtual environments that support cycle times down to 500μs for low-latency applications. For example, an injection molding machine containing a standard industrial PC can now be fitted with Nerve Blue software to run its injection pressure control, Human-Machine Interface (HMI), gateway, data analytics, and predictive maintenance functions all on the same device – delivering considerable hardware savings and aiding more efficient machine operation.
“We are very proud to offer the first commercial implementation of ACRN for the industrial market,” says Thomas Berndorfer, Member of the Executive Board, TTTech Industrial. “Nerve Blue already provides users a highly virtualized environment for running machine software on standard industrial PCs. Now with the integration of ACRN 2.0 we have been able to extend our platform to safely and securely host software for controlling the most critical elements within a machine. Nerve Blue together with ACRN 2.0 will make a real impact for our customers as they seek to improve machine efficiency and reduce costs.”
Nerve Blue is available today on Intel Atom processor E3900 series, Intel Celeron processor N3350, and Intel Pentium processor N4200 (Apollo Lake) platforms, 8th Generation Intel Core U-Series (Whiskey Lake) processors. Early next year, Nerve Blue will be available for Intel Atom x6000E Series and Intel Pentium and Celeron N and J Series Processors for Internet of Things (IoT) Applications (Elkhart Lake). A free trial-version of Nerve Blue can be accessed via www.tttech-industrial.com/try-nerve-blue. For a 30-day period, users can experience remote software management and virtualized application hosting for themselves without any need to download special software or set up hardware.
“This collaboration between TTTech Industrial, Intel and Project ACRN will enable the next generation of industrial solutions,” said Brian McCarson, Vice President and Sr. Principal Engineer, Internet of Things Group at Intel Corporation. “The powerful combination of Intel industrial hardware and software platforms and ACRN’s open-source, real-time hypervisor is bringing scalable and reliable solutions to the most demanding real-time applications.”
About the ACRN Project
ACRN is a flexible, lightweight reference hypervisor that is built with real-time and safety-criticality in mind. It is optimized to streamline embedded development through an open source platform. ACRN Project members include ADLINK, Aptiv, Intel Corporation, LGE, and Neusoft Corporation. To learn more about the project, visit projectacrn.org.
The Linux Foundation has registered trademarks and uses trademarks. For a list of trademarks of The Linux Foundation, please see its trademark usage page:www.linuxfoundation.org/trademark-usage. Linux is a registered trademark of Linus Torvalds.
Media Contact
Jennifer Cloer
Story Changes Culture
503-867-2304
jennifer@storychangesculture.com